Advanced Control Technology
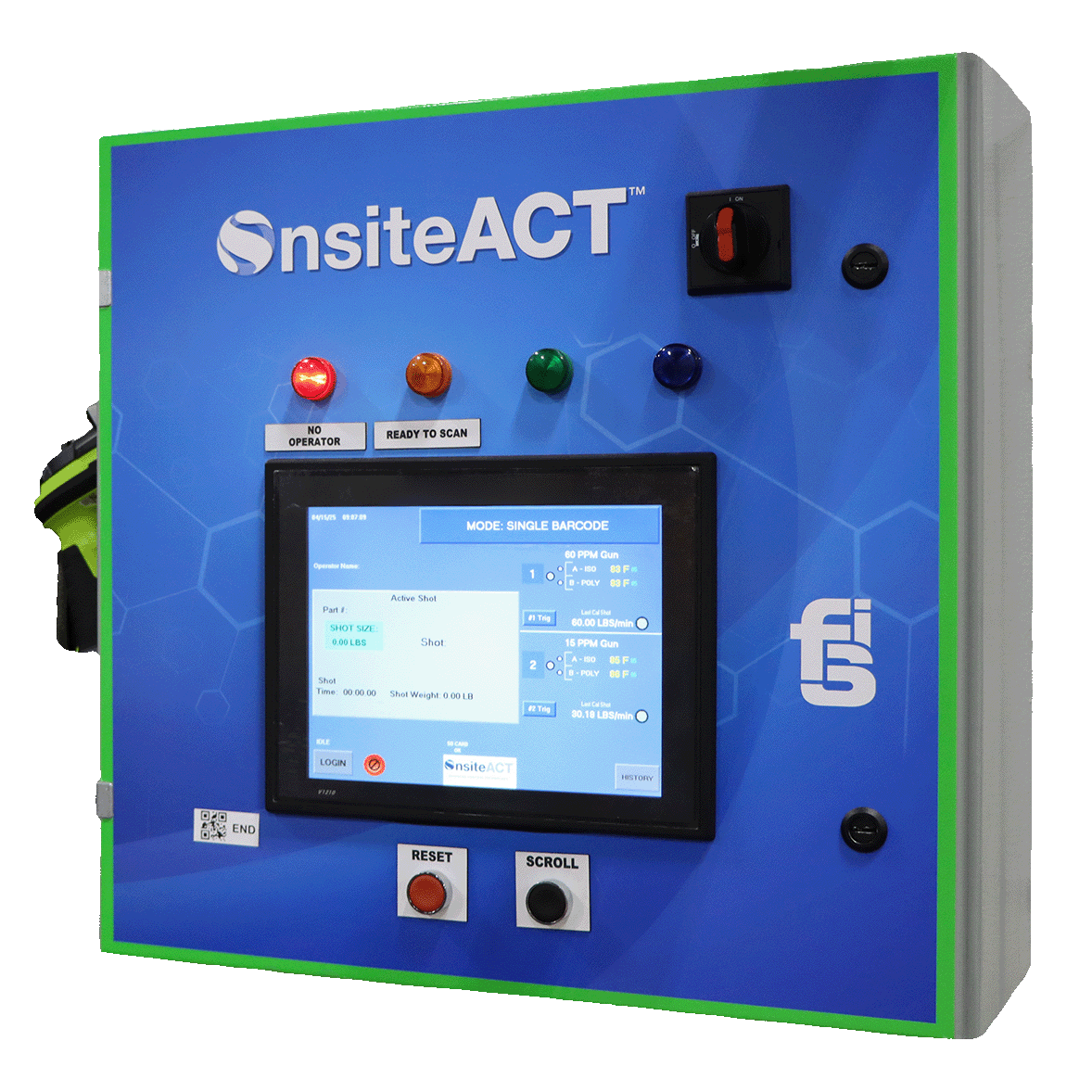

Onsite ACT is a complete foaming and quality assurance system that integrates quality checks, condition monitoring, QR code scanners, operator access control, and more to guarantee your operation works smoothly and effectively.
We developed the Onsite ACT with a thorough understanding of the polyurethane production process experience and collaboration with customers. Onsite ACT provides a full range of dispensing options that can meet your specific needs and manufacturing requirements.
Take the Guesswork Out of Filling Parts
Enhance your manufacturing with Onsite ACT. A system designed for precision, efficiency, and traceability.
KEY BENEFITS
- Powerful Insights
- Intuitive Interface
- Temperature Control
- Automatic Ratio Calculation
- Automatic Calibration
- Remote Access
- Data Download
CUSTOMIZED MODES
- Single Barcode
- Multi-Shot Barcode
- Timed Shot
- Manual Barcode Entry
- Manual Trigger
- Recipe Multi-Shot
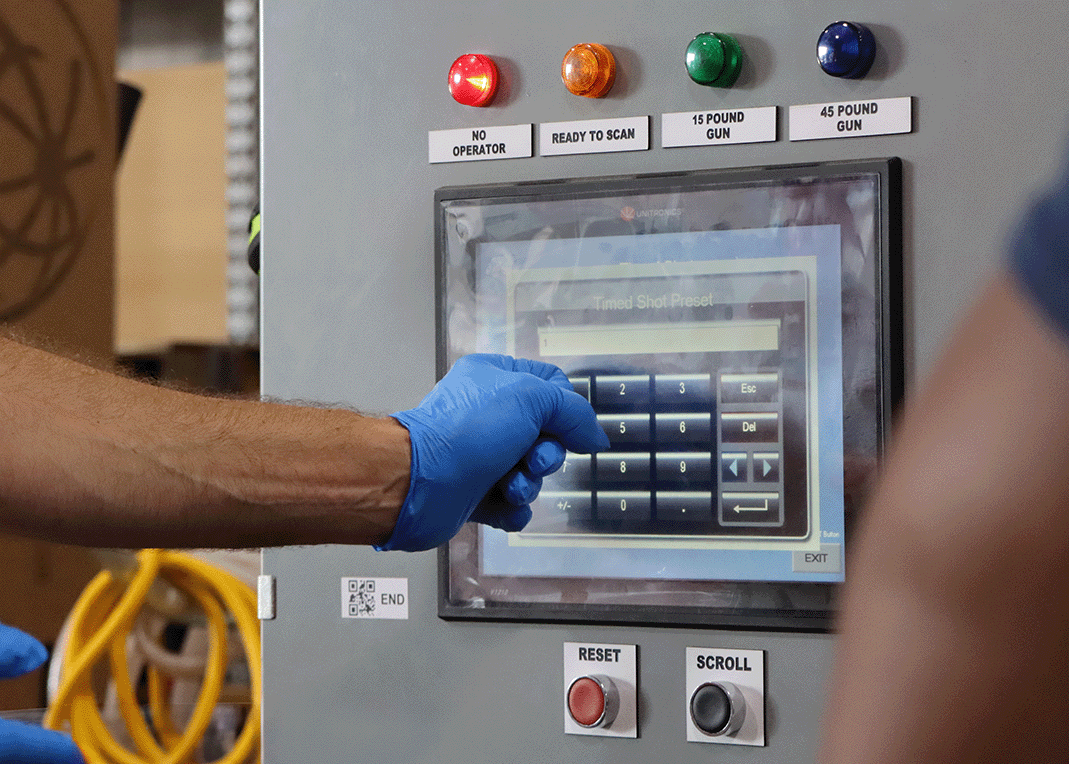
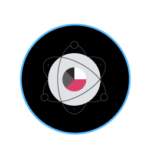
Data Collection
Automatically logs all shot, part, and crew information giving insight into the productivity and history of production.
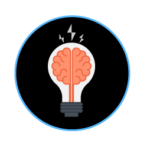
Intuitive Interface
Operator level employees can produce with a clear understanding of efficiency and focus on what matters most.
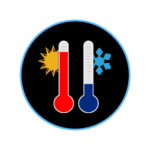
Temperature Controls
Provides real-time monitoring and tight controls of dispensing equipment temperatures through solid-state relays and high accuracy thermocouples.
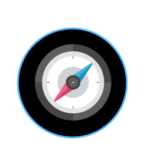
Auto-Ratio Calculation
PLC guided ratio sequence ensures that operators are performing checks at the proper times/intervals. The scale included with the equipment package makes hand calculations unnecessary. All ratio calculations are logged in perpetuity.
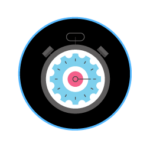
Auto-Calibration
The calibration sequence automatically adjusts shot times to ensure the correct weight, volume, and target in-place density of foam is shot into every part.
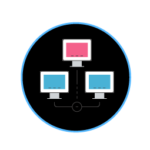
Remote Access
Can be monitored and adjusted via ethernet.
Global Reach.
Tailored Support.
Discover how Onsite ACT can make a difference in your manufacturing process.