IntelliQC is a user-friendly app designed to streamline the Quality Control process in production environments, replacing traditional pen-and-paper methods with a simple, efficient digital solution.
Accurate Data,
Reliable Production.
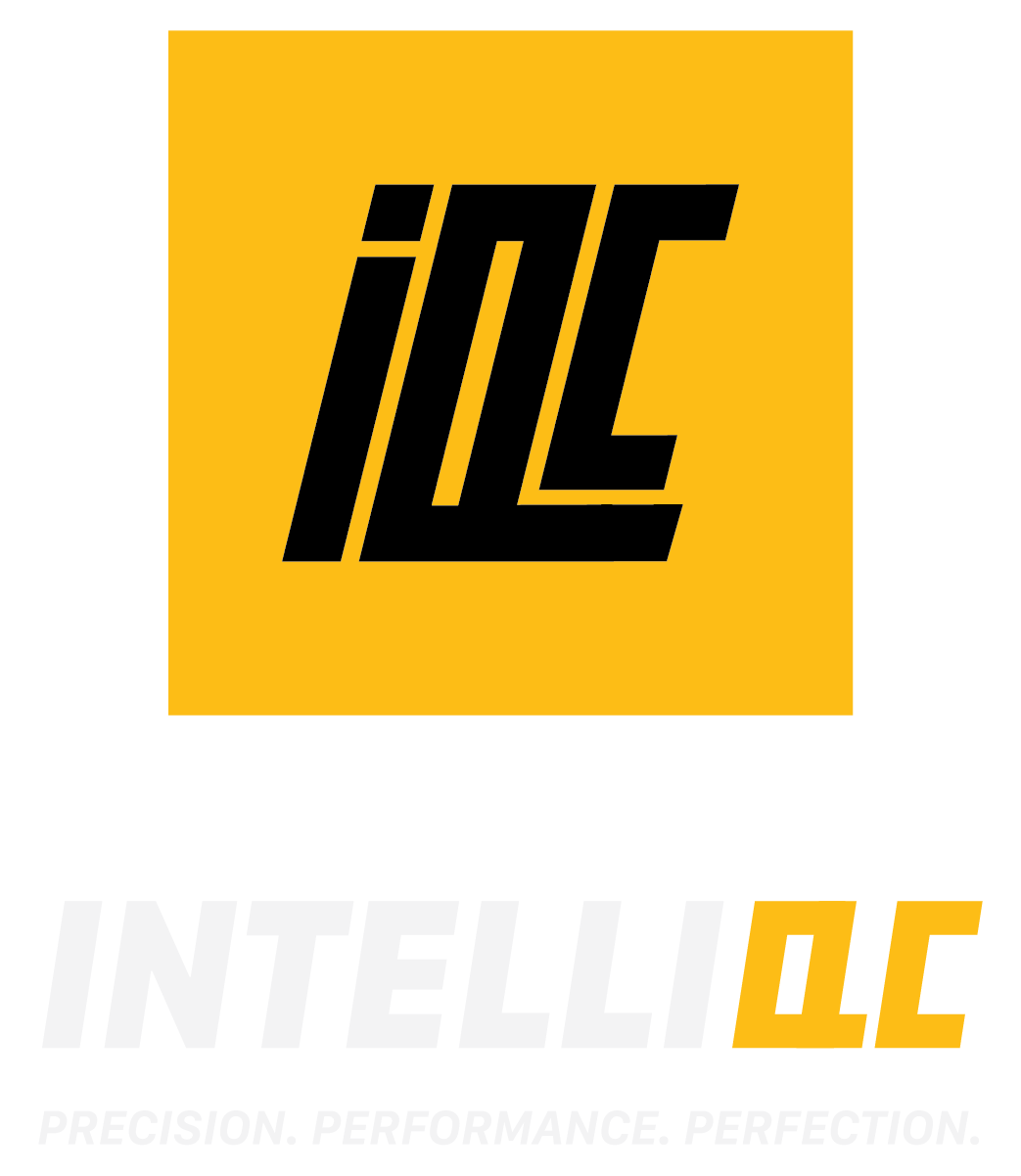
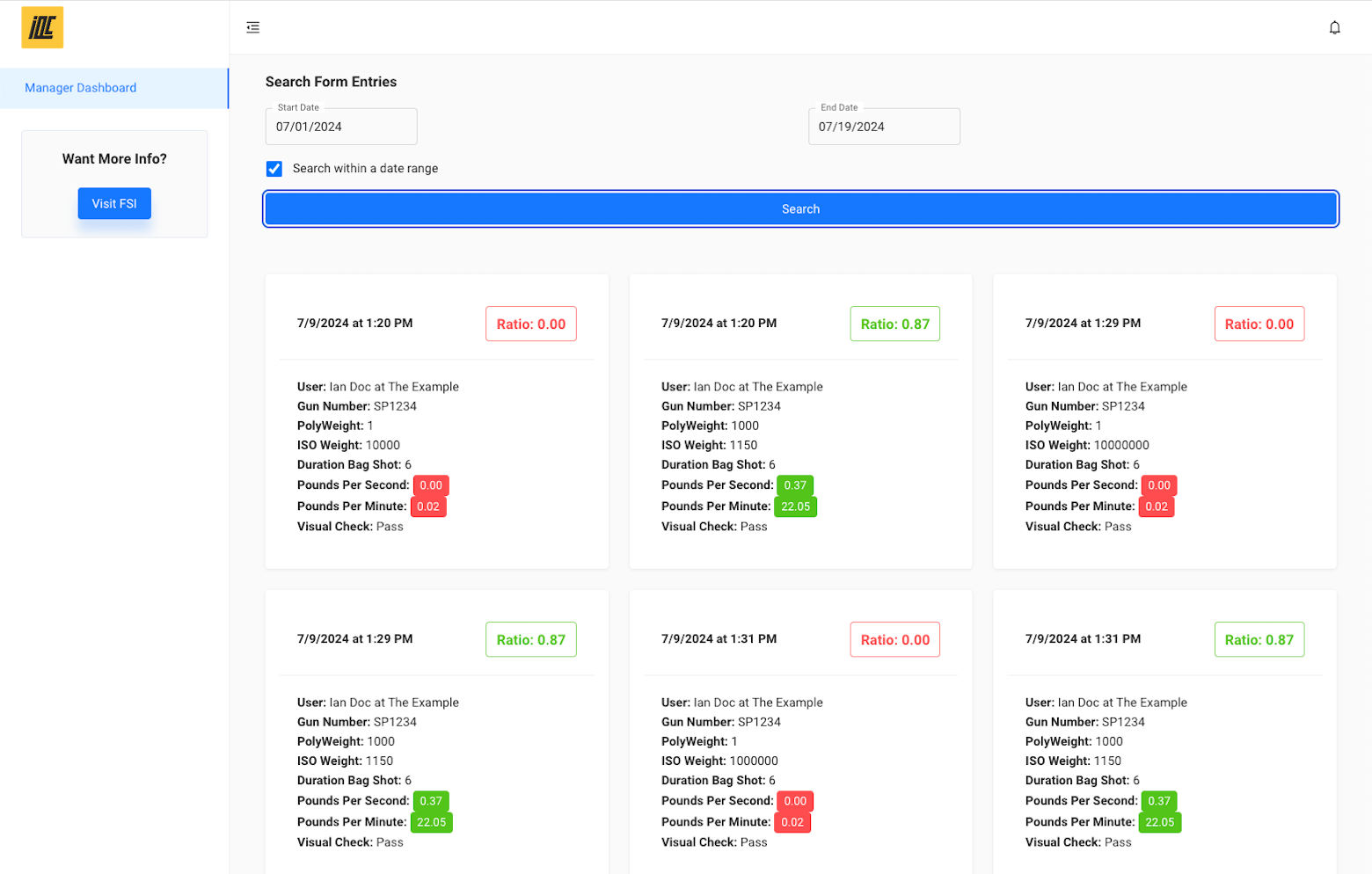
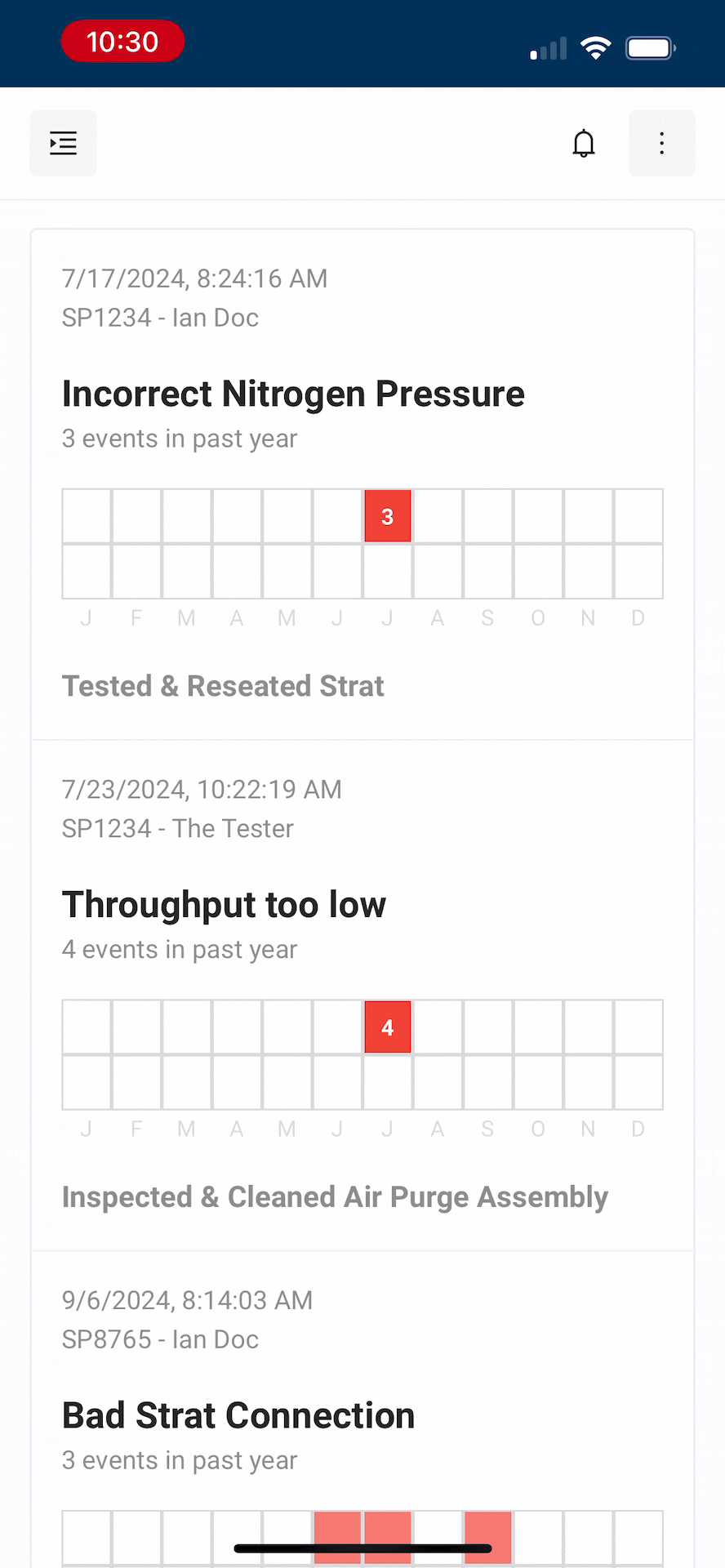
Ensure Quality Standards with IntelliQC by FSI
IntelliQC keeps years of QC records, helping managers identify trends and make proactive decisions. With real-time dashboard access, managers can continuously monitor and maintain production quality.
User Friendly, Streamlined Process
With just three simple fields to fill out on their phones, your production staff can now input QC data quickly and accurately. Managers gain access to real-time dashboard insights, ensuring that production quality is always maintained and never off ratio.
Managers are alerted if a user goes off-ratio. After troubleshooting, FSI’s Technical Services are notified automatically. If the issue persists, users receive manager and tech support contact details to quickly resolve problems, keeping your production line running smoothly.
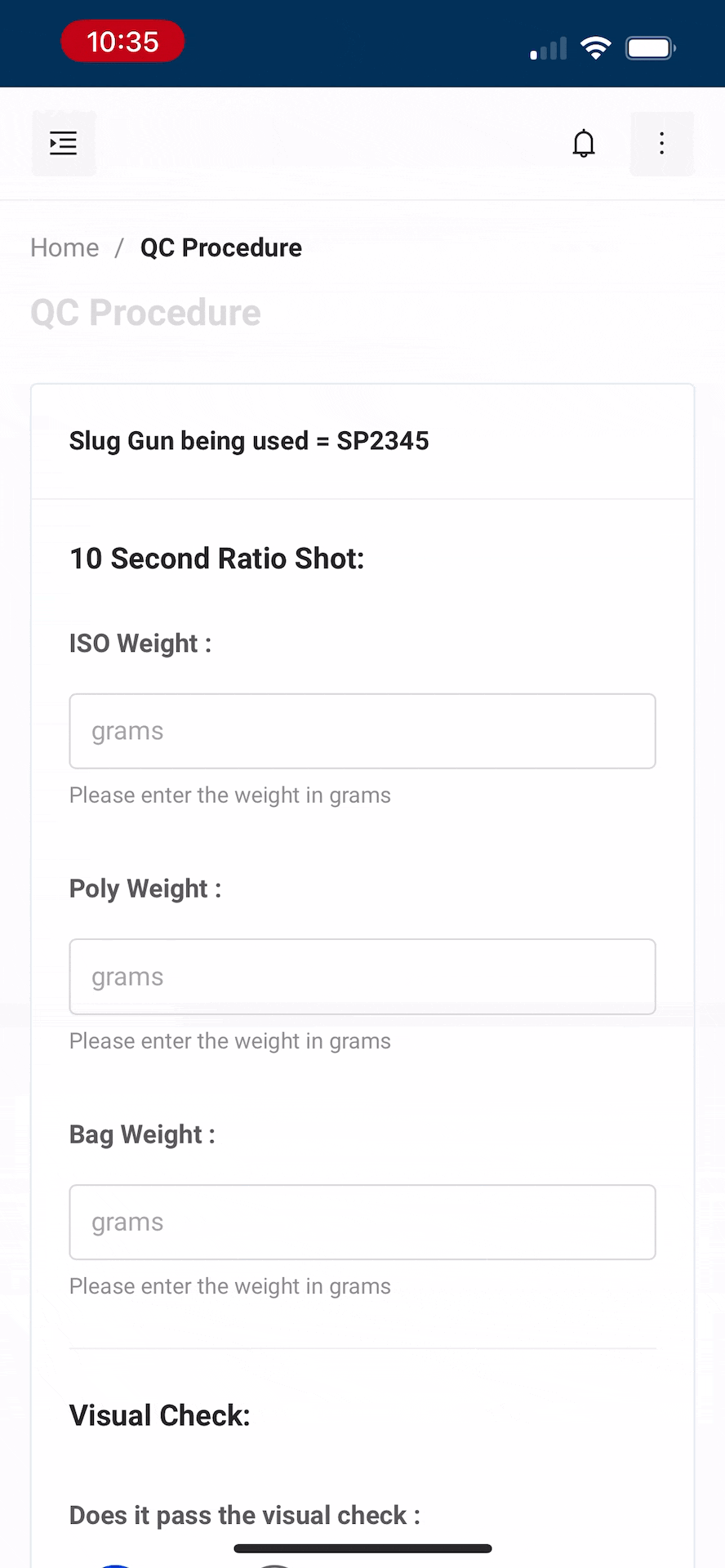
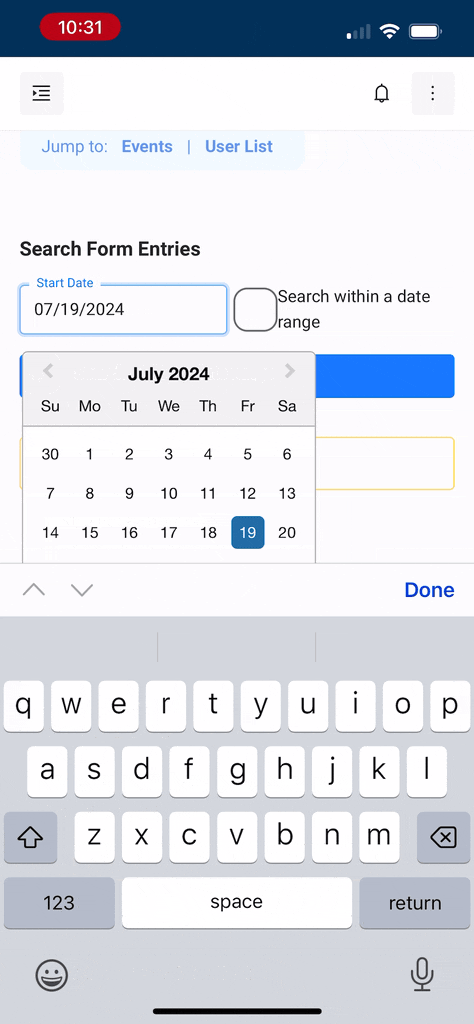
Accurate Data for Reliable Production
- Helps managers identify trends and make proactive decisions for improved production efficiency
- Minimizes the friction of filling out paperwork
- Ensures clean, reliable data
- Managers receive immediate updates only when off-ratio
- Empowers independent troubleshooting when off-ratio
Frequently Asked Questions
How does IntelliQC improve quality control?
IntelliQC minimizes the friction of filling out QC paperwork, ensures clean and reliable data, provides real-time updates to managers, and empowers production staff to troubleshoot issues independently.
How do I get IntelliQC?
You can get IntelliQC by contacting your Technical Representative or Account Manager. They’ll provide you with all the necessary information to start using the app.
How does IntelliQC help with long-term quality management?
IntelliQC securely maintains years of QC records, allowing managers to view trends and historical data. This comprehensive data archive empowers managers to identify patterns, predict potential issues, and make proactive decisions, enhancing production efficiency and reliability.
What happens if an off-ratio issue is detected?
If an off-ratio issue is detected, managers are alerted immediately. Production staff are guided through the troubleshooting process, and if the issue persists, they receive contact details for managers and tech support to resolve the problem quickly.
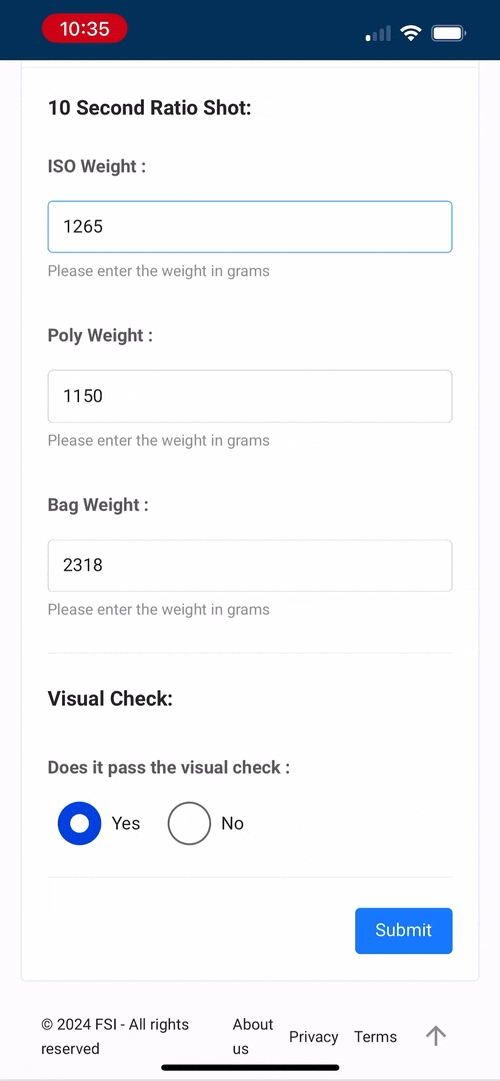
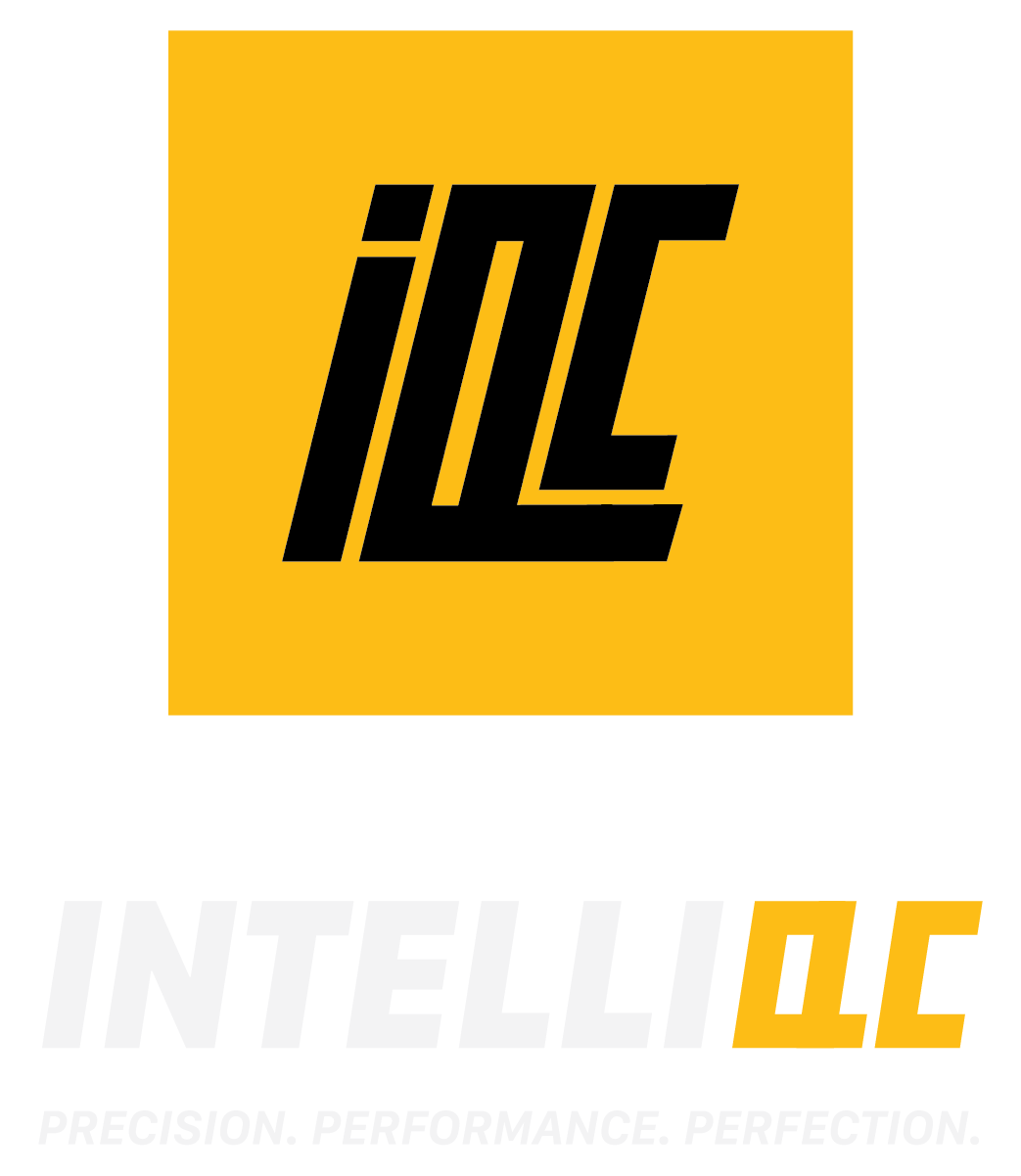