Spray foam insulation is essential for energy conservation, offering innovative solutions across various industries. FSI’s product range is designed to meet the needs of both large-scale professionals and DIY enthusiasts, delivering reliable, energy-efficient performance. Whether for commercial projects or home improvements, FSI provides versatile spray foam solutions to overcome insulation challenges.
Spray Foam: Elevating Energy Efficiency & Comfort
At FSI, we are committed to providing the best in energy efficiency and comfort through our expertly crafted spray foam solutions. As dedicated manufacturers, we don’t just produce products—we create effective solutions that improve homes and buildings everywhere.
We specialize in versatile, high-quality closed-cell spray foam, designed to meet the unique needs of contractors, architects, building owners, distributors, and DIY enthusiasts. Our expertise and commitment ensure that our spray foam solutions stand out in performance and reliability.
When you choose FSI, you’re not just investing in insulation; you’re joining a community dedicated to a more energy-efficient and sustainable future.
Spray Foam Insulation plays a significant role in energy conservation and can create unique opportunities for a diverse range of business owners, and even potential applications that are yet to be discovered or fully realized. Gain insights into the challenges faced by various sectors and learn how our comprehensive product range effortlessly overcomes these obstacles.
At FSI, our spray foam solutions are thoughtfully designed to accommodate a variety of needs, whether you’re a professional chasing superior insulation for large-scale endeavors or a DIY devotee in pursuit of energy-efficient enhancements for your home.
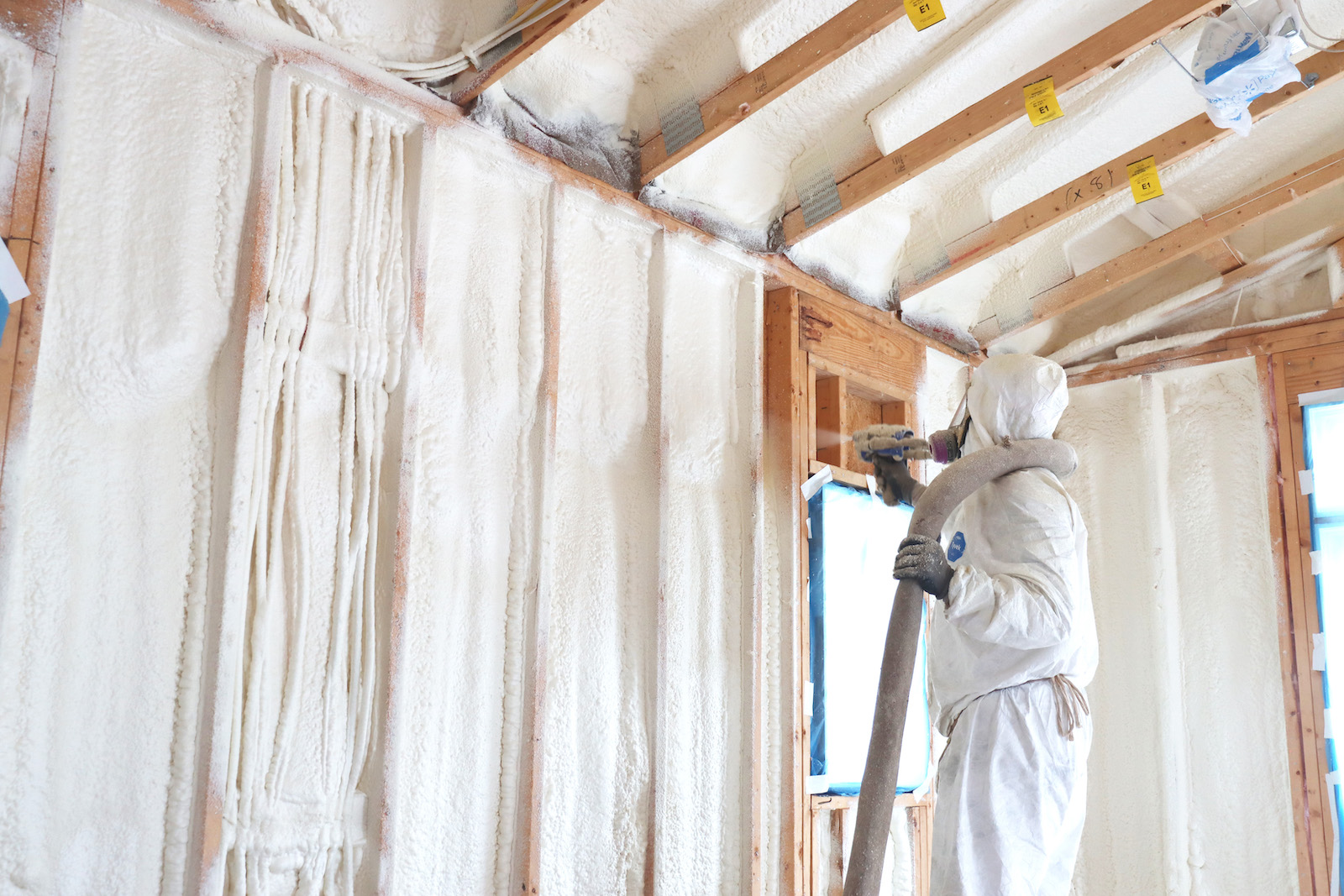
Spray Foam Products

Ecospray®
A closed-cell medium-density SPF system designed for industrial and OEM applications with a UL 94 HF-1 flammability rating and meets USCG requirements for flotation materials.
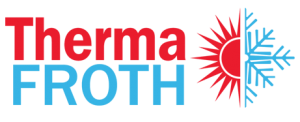
ThermaFroth®
A medium-density, low-pressure SPF system ideal for small jobs and patchwork applications. Delivered from disposable pressurized cylinder kits.
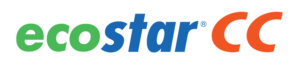
EcoStar® CC
High-performing spray polyurethane foam systems providing superior R-Value, excellent adhesion, rapid cure times, and are environmentally friendly.
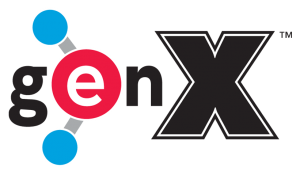
GenX™
An open cell spray foam, low-density system for insulating residential constructions, with near zero-GWP and excellent air sealing capability.
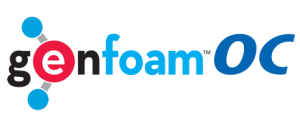
Genfoam™ OC
Similar to GenX™, an open-cell, low-density expanding spray foam system for insulating residential constructions. 100% water-blown, with near zero-GWP and excellent air sealing capability.
Custom Formulations
Whether your goal is to improve product quality, increase production efficiency, reduce environmental impact, lower costs, reduce scrap – or any combination of these and more – FSI is ready to help.
Types of Spray Foam
Open-Cell Spray Foam
Open-cell spray foam is a type of insulation that expands after installation to create small, open cells within the foam. This makes it softer and more flexible compared to closed-cell foam. Its structure allows it to fill nooks and crannies in walls, providing an effective air sealing property.
When considering spray foam insulation cost, Open Cell Spray Foam emerges as the less expensive choice. Additionally, open-cell spray foam has excellent sound-damping properties. Despite having a lower R-value (about 3.5 per inch), it is an effective insulation material and allows for bi-directional drying, preventing moisture accumulation within walls.
Open-cell spray foam is ideally used in interior walls and ceilings where soundproofing is desired. Its ability to conform to irregular shapes makes it an excellent choice for intricate framing details.
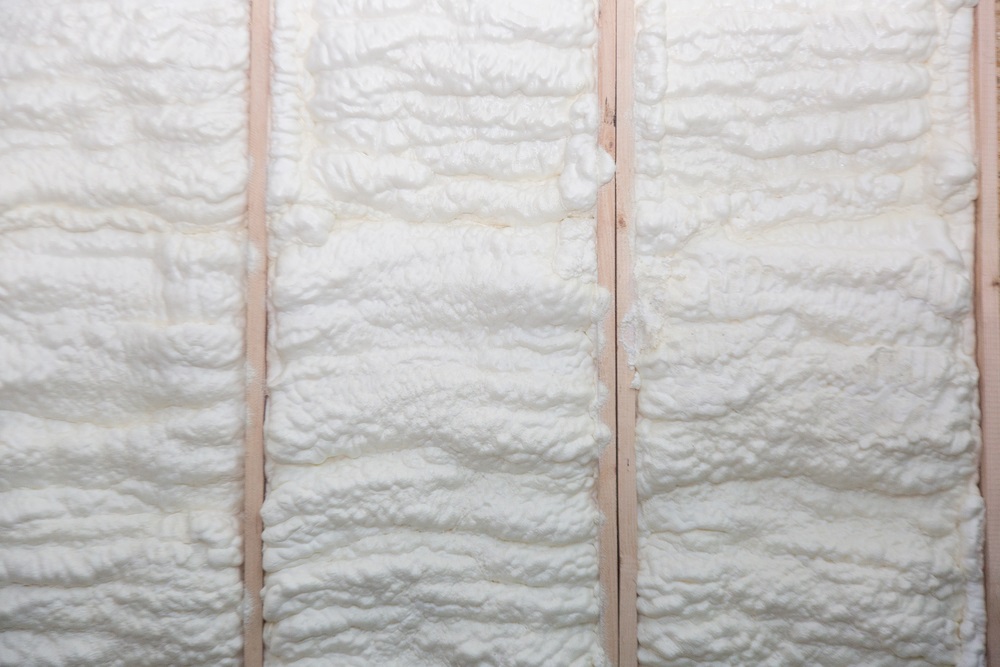
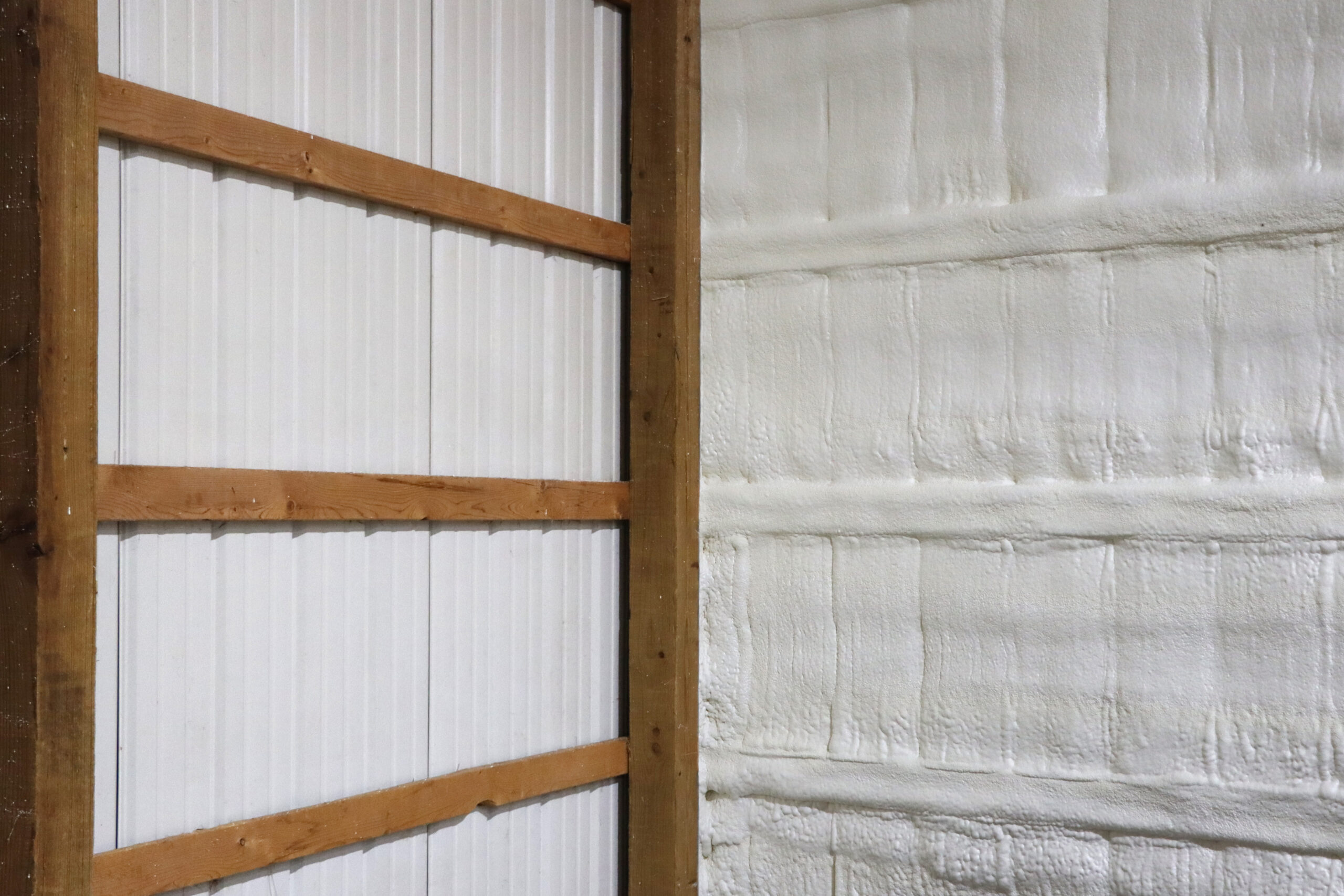
Closed-Cell Spray Foam
Closed-cell spray foam is a high-density insulation material with tiny, compact cells. This gives it a rigid structure, enabling it to provide added strength to the wall assembly, besides offering thermal insulation.
Closed-cell spray foam offers a higher R-value (about 6-7 per inch), making it a superior insulator. Its dense structure adds rigidity to walls, enhancing the overall structural integrity. Moreover, it is highly resistant to water and air infiltration, contributing to a healthier and more energy-efficient indoor environment.
Closed-cell spray foam is best suited for exterior walls, roofs, and areas that require superior insulation and water resistance. Its strength-enhancing properties make it an excellent choice for buildings in regions prone to severe weather conditions.
Structure
R-Value
Cost
Soundproofing
Water Resistance
Typical Applications
Benefits of Spray Foam Insulation
A Detailed Look at the Total Cost of Spray Foam Insulation
Lasting efficiency: superior insulation that enhances energy savings and structural strength.
Superior Insulating Properties
Spray foam insulation, especially closed-cell foam, boasts a high R-Value, making it a powerful insulator. It expands to fill gaps and cracks, providing a seamless insulation barrier. This ability to conform to irregular shapes allows it to effectively seal off air and moisture infiltration, ensuring a cozy and comfortable indoor environment.
Energy Efficiency
Spray foam insulation can significantly reduce your energy consumption, leading to substantial savings on utility bills. By providing an air-tight seal, it helps maintain a consistent temperature indoors, reducing the strain on your HVAC system. This energy efficiency is not just good for your wallet, but it also contributes to a sustainable and eco-friendly lifestyle.
Enhanced Structural Integrity
Closed-cell spray foam insulation does more than just insulate. Its dense and rigid structure adds strength to your walls, roofs, and floors, enhancing the overall structural integrity of your building. This added strength can be especially beneficial in areas prone to extreme weather conditions.
Long Lifespan
Spray foam insulation is designed to last. It maintains its performance over time, often outlasting the lifespan of the building itself. With spray foam insulation, you’re investing in a long-term solution that won’t sag or settle over time, providing consistent performance year after year.
Spray Foam Applications
Commercial
In commercial buildings, spray foam provides superior insulation, noise reduction, and air sealing, thereby improving energy efficiency and creating a more comfortable and productive work environment.
Industrial
For industrial applications, spray foam offers exceptional thermal and moisture protection, making it ideal for insulating large structures, equipment, tanks, and pipes, and ensuring durability even in harsh conditions.
Polyurethane Spray Foam FAQs
What is spray foam insulation?
Spray foam insulation is a high-performance material that is applied as a liquid and expands to form a solid, airtight layer. When sprayed, it expands rapidly, filling every crack, gap, and cavity in walls, ceilings, and floors. This expansion creates a seamless barrier that prevents air leaks, moisture infiltration, and the loss of heat or cool air, significantly improving energy efficiency in homes and buildings.
There are two main types of spray foam insulation: open-cell and closed-cell. Open-cell foam is softer and less dense, providing soundproofing and thermal insulation. Closed-cell foam, on the other hand, is denser and more rigid, offering higher R-values (thermal resistance) and providing additional structural strength. Both types of spray foam help to reduce energy consumption, lower heating and cooling costs, and improve indoor comfort by maintaining a consistent temperature.
Spray foam insulation also helps with moisture control, preventing mold and mildew growth, and enhancing the overall durability of a building. It is commonly used in residential, commercial, and industrial applications due to its versatility and effectiveness in insulating irregular or hard-to-reach areas.
What is the chemical structure of polyurethane foam?
The chemical structure of polyurethane foam is the result of a polymerization process involving two primary components: isocyanates and polyols. When combined, these materials undergo a chemical reaction known as a condensation or addition polymerization, which forms the structure of polyurethane foam.
- Isocyanates: These are organic compounds containing the isocyanate group (-N=C=O), a highly reactive chemical group. The most common isocyanates used in the production of polyurethane foams are methylenediphenyl diisocyanate (MDI) and toluene diisocyanate (TDI). These isocyanates react with polyols to form urethane bonds.
- Polyols: Polyols are compounds that contain multiple hydroxyl groups (-OH). They are usually derived from petrochemical sources like propylene oxide or ethylene oxide, or from renewable resources. Polyols can be either flexible (used in soft foams) or rigid (used in hard foams), and their structure plays a significant role in the foam’s properties, including flexibility, durability, and thermal insulation.
When the isocyanate reacts with the polyol, the two compounds undergo a polyaddition reaction, resulting in the formation of a urethane linkage (–NH–C(O)–O–). This reaction leads to the creation of a long-chain polymer network. The process typically involves the use of a blowing agent (which can be water, a gas, or another substance) that helps the reaction expand the mixture into foam, creating tiny gas bubbles trapped within the structure. These bubbles give the foam its characteristic lightweight, insulating, and cushioning properties.
Chemical Structure Overview:
•The primary repeating unit of polyurethane foam is the urethane linkage (–NH–C(O)–O–).
•The foam’s structure is made up of long polymer chains formed by the repeated bonding of isocyanates and polyols.
•The presence of cross-links between the polymer chains (especially in rigid foams) adds to the strength and stability of the foam.
•Blowing agents contribute to the foam’s formation by generating gas bubbles, which get trapped in the polymer matrix, giving the foam its characteristic spongy, cellular structure.
In the case of flexible polyurethane foams, the polymer chains are less rigid and have more open spaces between them, which makes the foam soft and flexible. Rigid polyurethane foams, on the other hand, have a denser, more tightly bound polymer network, offering higher structural strength, insulation properties, and resistance to moisture and heat.
The properties of polyurethane foam—such as its density, rigidity, and insulation capacity—can be controlled by varying the ratios of isocyanates to polyols, the choice of polyols, and the type of blowing agents used during the production process. This versatility allows polyurethane foam to be used in a wide range of applications, from insulation in buildings to cushioning in furniture and packaging.
How is polyurethane foam produced?
Polyurethane (PU) foam is produced through two primary methods: slabstock foam production and liquid injection foam production. Each method is tailored for different applications and results in foams with unique properties.
Slabstock Foam Production:
In slabstock foam production, a polyurethane mixture is poured onto a continuous production line, forming large sheets or blocks of foam. This method is ideal for producing high-volume foam products like mattresses, cushions, and insulation.
Process Overview:
- Raw Materials: Polyols, isocyanates, blowing agents, and other additives are mixed together.
- Mixing: The chemicals react to form urethane links, with the blowing agent creating a cellular structure.
- Foam Formation: The mixture is poured onto a conveyor, where it expands into a continuous sheet or block.
- Curing: The foam is cured to harden and achieve its final form.
Advantages:
- Suitable for high-volume production.
- Versatile and cost-effective for mass production.
Disadvantages:
- Limited to larger foam products.
- Slower production for custom shapes.
Liquid Injection Foam Production:
Liquid injection foam, or molded foam, involves injecting a liquid polyurethane mixture into a mold, where it expands and takes the shape of the mold. This method is used for producing more complex shapes or small, precise parts.
Process Overview:
- Preparation: Raw materials are mixed with specific ratios for molding.
- Injection: The mixture is injected into a closed mold, where it reacts and expands.
- Curing: The foam cures within the mold.
- Cooling and Ejection: Once cured, the foam is cooled and ejected from the mold.
Advantages:
- Suitable for complex shapes and precise parts.
- Faster production for small to medium parts.
Disadvantages:
- Requires molds, which can increase tooling costs.
- Not ideal for large-scale production.
Key Differences:
- Material Properties: Slabstock foam has uniform density, while liquid injection foam can be tailored for specific properties.
- Production Speed: Slabstock is faster for bulk production; liquid injection is faster for custom parts.
- Applications: Slabstock is used for large sheets, while liquid injection is better for small, customized components.
Both methods offer flexibility, allowing manufacturers to choose the right process based on product requirements, ensuring optimal foam performance and meeting specific design or functionality needs.
How strong is polyurethane foam?
Polyurethane (PU) foam strength varies depending on factors like density, formulation, and intended use. Generally, PU foam is known for its resilience and durability, but its strength can differ based on these variables.
Key Factors Influencing PU Foam Strength:
- Density: Higher-density foam is stronger and more rigid, offering better structural support. It is commonly used in applications like insulation and automotive components. Lower-density foam is softer and more flexible, suitable for cushioning and comfort but less structurally strong.
- Formulation: The specific chemicals used, such as polyols and isocyanates, affect the foam’s mechanical properties. PU foams can be engineered to be flexible, rigid, or impact-resistant, depending on the application.
- Cell Structure: Closed-cell foam is stronger and more durable than open-cell foam because the cells are sealed, offering greater resistance to moisture, air infiltration, and compressive forces. Closed-cell foam is commonly used in structural applications, while open-cell foam is more flexible and provides sound absorption.
Applications and Strength:
- Compressive Strength: High-density PU foam used for structural insulation or in automotive parts has excellent compressive strength, resisting deformation under pressure.
- Impact Resistance: PU foam is highly impact-resistant, making it ideal for applications like seat cushions or protective packaging.
- Durability: With its ability to maintain shape and strength over time, PU foam is an excellent long-term solution for insulation and other structural uses.
In summary, PU foam’s strength depends on its density, formulation, and cell structure. It is a versatile material that can be tailored to provide high strength, durability, and impact resistance for various applications, from insulation to cushioning.
What is polyurethane used for?
Polyurethane (PU) foam is a versatile material used across various industries due to its durability, flexibility, and insulating properties. Common applications include:
- Cushioning and Upholstery: Used in furniture, mattresses, and automotive seating for comfort and support.
- Thermal Insulation: Found in construction, refrigeration, and HVAC systems for energy efficiency and temperature control.
- Soundproofing: Utilized in acoustic panels, wall and ceiling insulation to reduce noise transmission.
- Impact Protection and Energy Absorption: Used in protective gear, packaging materials, automotive parts, and sports equipment for safety.
- Packaging Materials: Provides lightweight, protective packaging for fragile items.
- Building and Construction: Used for insulation in walls, roofs, and floors to enhance energy efficiency in residential and commercial buildings.
- Automotive: Applied in automotive seating, sound insulation, and structural parts for comfort and safety.
Its adaptability makes polyurethane foam an essential material in various sectors, providing both functional and environmental benefits.
Is polyurethane foam environmentally friendly?
Polyurethane foam can be environmentally friendly, especially when using sustainable alternatives like FSI’s Ecomate® blowing agent. Ecomate® is a patented, zero-GWP (Global Warming Potential) and non-VOC (Volatile Organic Compounds) solution, making it a more environmentally conscious option compared to traditional foam formulations.
Additionally, polyurethane foam’s exceptional insulating properties help reduce energy consumption in buildings, refrigeration, and transportation, contributing to energy conservation and lower carbon footprints over time. Although traditional polyurethane foam can have environmental impacts, the use of eco-friendly alternatives like Ecomate® and advancements in recycling processes are making it a more sustainable option for a variety of applications.
Polyurethane foam is also durable and has a long life cycle, which reduces the need for frequent replacements and minimizes waste.
Are there any health risks associated with polyurethane foam?
Generally speaking, polyurethane foam itself does not pose significant health risks when used appropriately. However, there are some considerations to keep in mind, particularly during the manufacturing process or installation.
Potential Risks:
- Diisocyanates: These are chemicals used in the production of polyurethane foam, and they can be hazardous if inhaled or if they come into prolonged contact with skin. Diisocyanates may cause respiratory irritation, skin rashes, or other allergic reactions in some individuals, particularly those with existing sensitivities or asthma.
- Dust and Fumes: During the foam cutting, sanding, or shaping processes, small amounts of foam dust or fumes can be released. Inhalation of excessive foam dust can irritate the respiratory system. Proper ventilation and wearing protective equipment (such as masks or respirators) can help mitigate this risk.
Safety Measures:
- Using appropriate personal protective equipment (PPE) such as gloves, goggles, and respirators can reduce exposure to potentially harmful substances.
- Ensuring proper ventilation when handling polyurethane foam or during its application is essential, especially in enclosed spaces.
- After the foam has fully cured, it is generally considered safe for normal use in household or commercial environments.
What are the 2 main types of polyurethane foam?
The two main types of polyurethane foam are flexible foam and rigid foam:
- Flexible Foam: This type of polyurethane foam is primarily used in applications where cushioning and comfort are needed. It is commonly found in products such as mattresses, upholstered furniture, automotive seating, and pillows. Flexible foam is soft, adaptable, and provides excellent support and comfort.
- Rigid Foam: Rigid polyurethane foam is known for its insulating properties and is used primarily for thermal and sound insulation. It is commonly found in construction materials such as insulation boards, spray foam insulation for roofs and walls, and in refrigeration. Rigid foam is strong, durable, and helps improve energy efficiency by reducing heat loss or gain.
What is a polyurethane systems house?
Polyurethane systems houses provide comprehensive solutions for producing polyurethane chemical systems, utilizing state-of-the-art production processes and customized options to ensure projects are executed with precision and accuracy.
Will spray foam stop water?
Yes, spray foam insulation can stop water and prevent outside moisture from entering your home. Spray foam is water-resistant and can be completely waterproof depending on its type. The higher density of closed-cell foam makes it a great vapor barrier and can reduce moisture and mold issues in attics and crawl spaces.
Spray foam can also seal off small gaps where moisture can enter your home by forming an airtight seal at the base of the wall or ceiling.
Why is spray foam insulation so expensive?
Spray foam is expensive because of the materials, equipment, and training required to install it. It’s not as simple as picking up some insulation at the hardware store, and requires hiring a professional team to bring their spray foam machine. Spray foam can also cost more than other types of insulation, such as fiberglass, because it takes more time to install.
Spray foam insulation can cost up to $1 per square foot. While it costs more up-front than traditional insulation, it can lead to big savings on heating and cooling costs over time. Its highly effective heat retention means you don’t need to use as much energy to heat your home, which could save you up to 50% on your energy bills.
Where can I buy bulk spray foam insulation
Our team of spray foam insulation experts can help you find the products you need, no matter the size or complexity of the job. We custom blend the foam you need in house, so our inventory is among the largest in the world with a distribution network to get you what you need, when you need it. FSI is among the leading wholesale spray foam insulation suppliers globally, and can help you whether you’re just getting started or a seasoned expert.